
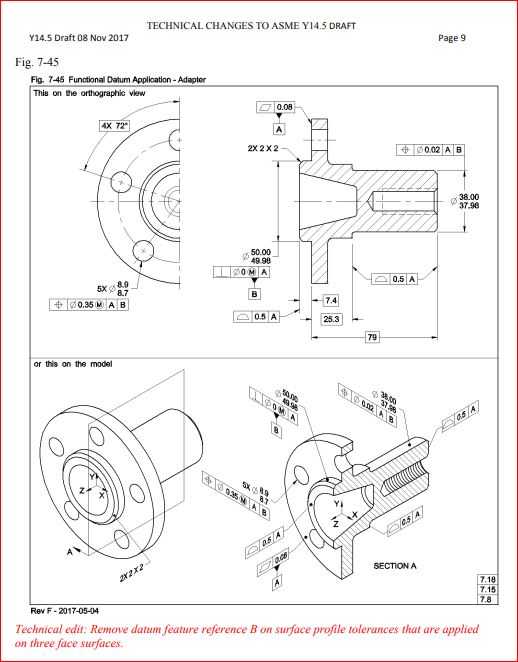
Then how can MBD implementers answer these challenges? One recommendation to ease the MBD data consumption is to organize and present the 3D annotations clearly. While in 3D, technically speaking, you can fully define an entire model in one viewport and rotate the model to present the data. So each view is less likely to become too busy. The reason is that the 2D nature of drawings has to rely on multiple perspectives to present the information separately,such as front, top and right views. To be fair, the crowded annotation display happens to both 2D and 3D, but just occurs more often in 3D than in 2D.

After the annotations are added, the busy display can make it hard, or even overwhelming, for downstream data consumptions as shown in Figure 1.
#Asme y14.5 2009 solidworks software#
Why should I bother with 3D annotations?” This objection may become more pressing since 2D drawing tools have been perfected for the past 20 or 30 years, while MBD software applications are relatively new and less developed. Because most engineers are more familiar with 2D detailing tools than with 3D annotating techniques, a frequent objection is that “I can detail it much faster in 2D drawings. A crowded display of a 3D annotated model.Īnnotating a 3D model can take anywhere from several minutes to dozens of hours, depending on the model complexity, the required level of details and a user’s skills. It’s difficult not only for the data authors to create, but also for the recipients to interpret.įigure 1. Figure 1 shows an example of busy 3D annotations. Special emphasis on aerospace, automotive, medical device, precision instrumentation and related industries.In model-based definition (MBD) implementations, a common challenge is that 3D annotations can take a lot of time to call out explicitly and, as a result, can quickly crowd the graphics display. Intended for design, drafting, mechanical, manufacturing, production, tool/gage, quality, process and project engineers, CAD/CAM/CAE specialists, inspectors and educators across a broad range of global manufacturing. By providing uniformity in drawing specifications and interpretation, GD&T reduces guesswork throughout the manufacturing process - improving quality, lowering costs, and shortening deliveries. GD&T is an essential tool for communicating design intent - that parts from technical drawings have the desired form, fit, function and interchangeability. This standard establishes industry practices for stating and interpreting dimensioning and tolerancing or "GD&T" and related requirements for use on engineering drawings and related documents. The ASME Y14.5-2018 standard is the only dimensioning and tolerancing guideline for the design language of geometric dimensioning and tolerancing (GD&T.) within the United States. Please not that I make no claim as to which standard may or may not be better or is preferred. This document is my first effort to details the changes and edits between ASME Y14.5-2009 and ASME Y14.5-2018. According to my copy of the standard, it was released for purchase in about January of 2019.
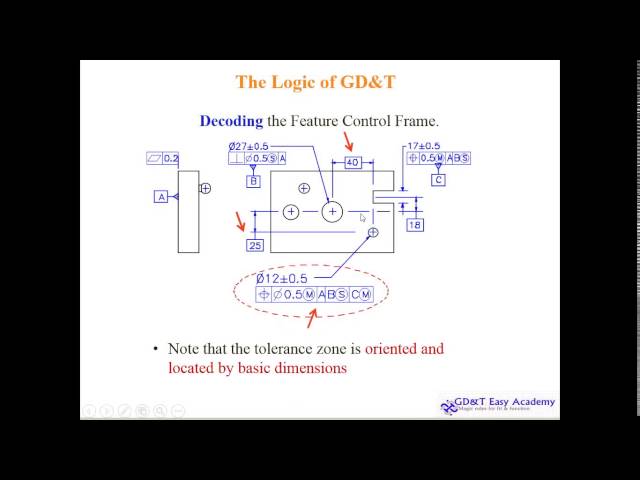
The ASME Y14.5-2018 was approved for release in November of 2018. Open: Differences Between ASME Y14.5-2009 and ASME Y14.5-2018 This resource requires a Premium Membership

